opening work in process inventory formula
Deduct the cost of raw material from this figure that is on hand at the end of the accounting period to determine the costs of materials consumed during the accounting period. Budgeted sales qty x sp.
Inventory Raw Materials Work In Progress And Finished Goods
Finally you should subtract the amount of inventory purchases from your result.
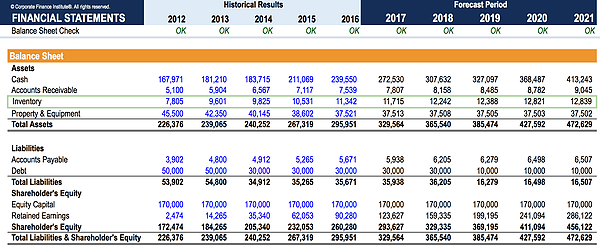
. Beginning WIP Manufacturing costs - Cost of goods manufactured. Ending inventory Previous accounting period beginning inventory Net purchases for the month COGS. FIFO method assumes that those units which represent work-in-progress at the beginning are completed first and the units partly complete at the end of the period are units introduced or transferred from the preceding process during the current period.
Amount of Goods in Stock x Unit Price Ending Inventory. A work in process or WIP for short is the term that refers to any inventory thats been initiated into production but hasnt been completed by the end of a companys accounting cycle. The factory overhead costs can be calculated for the accounting period.
Determine the cost of goods sold COGS using your previous accounting periods records. Any raw material inventory that has been combined with human labor but is not yet finished goods inventory is work in process inventory. Accounting with Opening and Closing Work-in-Progress-FIFO Method.
Once the manufacturer starts the production process those items are no longer raw materials. Therefore the direct labour and the operational cost of putting the kettle together would be classified under work in. Cost of opening.
COGS Ending Inventory Purchases. The work-in-process inventory that a company has started but not completed has specific value. This means the beginning inventory is 400000 at the start of the accounting period.
The opening balance in the Process Work-in-Progress a. That makes it a part of manufacturing inventory see. 8000 240000 238000 10000.
24000 20000 44000. Work in progress WIP sometimes referred to as work in process is the sum of all costs put into the production. Cost of Goods manufactured Direct materials cost Direct labor cost Factory overhead cost Opening work in process inventory Ending work in process inventory.
Every dollar invested in unsold inventory represents risk. Ending Inventory Beginning Balance Purchases Cost of Goods Sold. Work in process inventory examples.
Beginning WIP Inventory Manufacturing Costs COGM Ending WIP Inventory. You have a lot of different situations that can happen in your organization that may lead to this. Manufacturing Price x Quantity Purchases.
The formula for this is as follows. It is important that your bookkeeping shows all of the costs in order to come up with your final cost. As far as the calculations are concerned the formula for calculating work in process is.
Cost of goods manufactured. Higher sales and thus higher cost of goods sold leads to draining the inventory account. Work in process operating inventory goods in process raw material used during the period direct labor during the period factory overhead for.
Thus we can now calculate beginning inventory using the formula. The work in process inventory refers to the part of the production cycle of turning your individual raw materials into a kettle. 500000 250000 350000 400000.
It is one of the inventory accounts commonly used to track the flow of costs in a. The labor costs for the accounting period should be calculated. WIP Inventory Example 2.
Ending work in process. The work in process formula is. For example you have run out of materials to create a certain amount of products.
During the remaining financial year the company has made purchases amounting 20000 and during that time on the companys income statement the cost of goods sold is 40000. During the year 150000 is spent on manufacturing costs along with your total cost of finished goods being 205000. The calculation of ending work in process is.
As a result of this you would have to freeze the production process until you have bought the materials to use. This product value is important for financial reporting. Let say company A has an opening inventory balance of 50000 for the month of July.
Production in terms of. WORK IN PROCESS INITIAL WORK IN PROCESS DIRECT LABOR OVERHEAD - COST OF FINISHED GOODS. Below is the data table.
The standard work in process inventory definition is all the raw material overhead costs and labor associated with every stage of the production process. Next you should add up the calculated ending inventory cost and the CoGS value. Work in process inventory refers to the total cost of unfinished goods currently in the production process at the end of each accounting period.
To find the amount of inventory purchases multiply the amount of bulbs. This account represents the costs of resources used but not yet turned into completed products. As determined by previous accounting records your companys beginning WIP is 115000.
Ending Work in Process WIP Inventory COGM. Opening work-in-process inventory closing work-in-process inventory cost of goods manufactured. 500 x 700 350000.
1200 x 20 24000. Formulas to Calculate Work in Process. Additionally items that are considered work in progress may depreciate or face a lower demand from consumers once they have been completed.
COGS Previous accounting period beginning inventory previous accounting period purchases previous accounting period ending inventory. The amount of ending work in process must be derived as part of the period-end closing process and is also useful for tracking the volume of production activity. The work-in-process inventory account is an asset account that is used to track the cost of the partially finished goods.
Inventory Formula Example 1. Work In Progress - WIP. In accounting a work in progress WIP account is an inventory account that includes goods that are in the process of being produced but are not yet finished.
It is also considered a current asset on a companys balance sheet. The conceptual explanation for this is that raw materials work-in-progress and finished goods current assets are turned into revenue. Lets break down the steps for how to find beginning inventory.
The work in process inventory formula is the Beginning WIP Inventory Manufacturing Costs COGM. Do the same with the amount of new inventory.
Inventory Formula Inventory Calculator Excel Template
Cost Of Goods Manufactured Formula Examples With Excel Template
Wip Inventory Definition Examples Of Work In Progress Inventory
Ending Inventory Formula Calculator Excel Template
Work In Process Wip Inventory Youtube
Inventory Ratio Definition Formula Step By Step Calculation
How To Calculate Ending Inventory The Complete Guide Unleashed Software
Finished Goods Inventory How To Calculate Finished Goods Inventory
What Is Inventory Turnover Inventory Turnover Formula In 3 Steps
Compute The Cost Of A Job Using Job Order Costing Principles Of Accounting Volume 2 Managerial Accounting
Manufacturing Account Format Double Entry Bookkeeping
Finished Goods Inventory How To Calculate Finished Goods Inventory
Inventory Formula Inventory Calculator Excel Template
3 Types Of Inventory Raw Materials Wip And Finished Goods Youtube
How To Calculate Finished Goods Inventory
Cost Of Goods Manufactured Formula Examples With Excel Template
What Is Work In Process Wip Inventory How To Calculate It Ware2go